The Expanded Group provides a total capability in the early construction phases of major projects, providing an end-to-end solution or a bespoke choice of services, backed by a central technical design and engineering resource.
Boasting a directly employed workforce of almost 1,300 operatives and over 400 staff, we know we can deliver. Working as ‘one team’ we have the ability to design, manufacture and install precast components through our own manufacturing facility; we can supply plant, small tools, accommodation and tower cranes through our partner company Select Plant Hire, and provide stone and stone cladding services from Vetter UK.
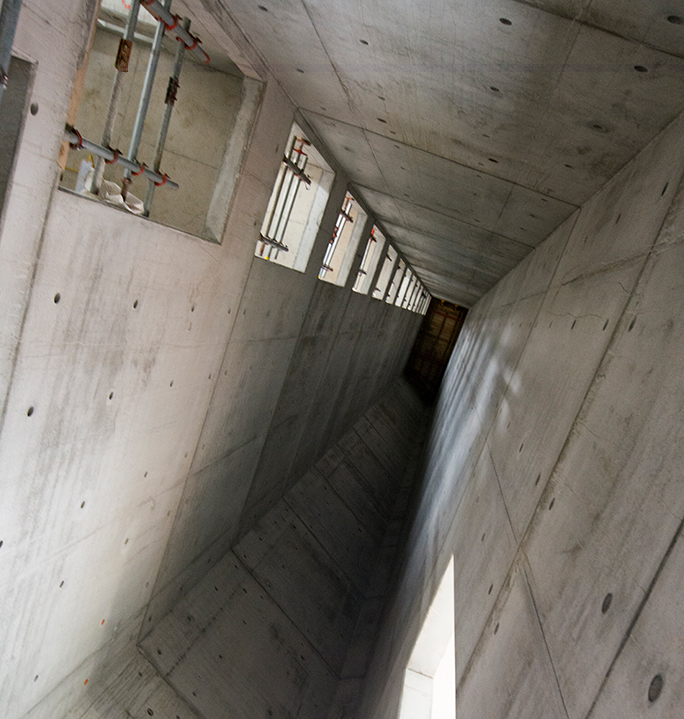
The Expanded Group provides a total capability in the early
construction phases of major projects, providing an end-to-end
solution or a bespoke choice of services, backed by a central
technical design and engineering resource.
Our services include:
- Infrastructure
- Groundworks
- Substructures
- Superstructures
- Precast facades
- Specialist engineering
This diverse capability streamlines the delivery process by enabling us to undertake works directly – reducing the time and cost implications associated with multiple handovers between different trades/packages.
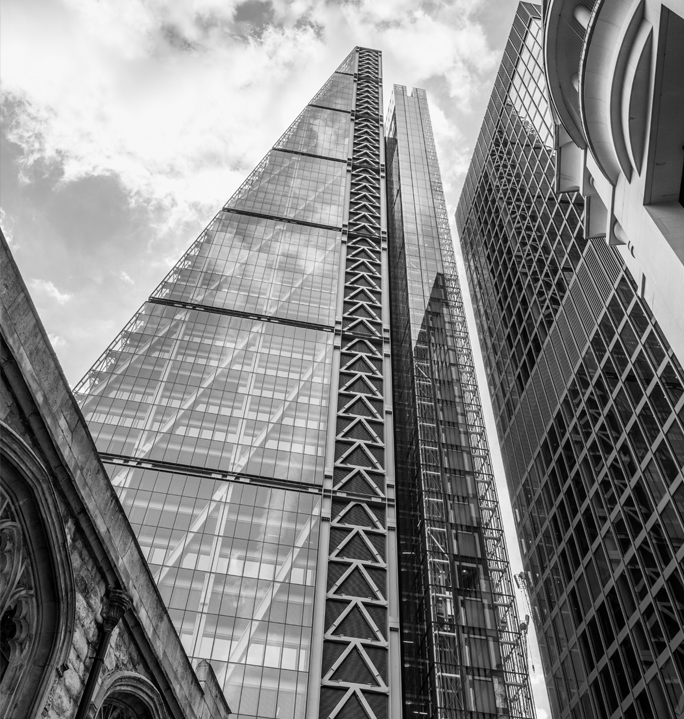
Boasting a directly employed workforce of almost 1,300 operatives and over 400 staff, we know we can deliver. Working as ‘one team’ we have the ability to design, manufacture and install precast components through our own manufacturing facility; we can supply plant, small tools, accommodation and tower cranes through our partner company Select Plant Hire, and provide stone and stone cladding services from Vetter UK.
We also offer a highly skilled temporary works department, materials technology centres in Manchester and London, geotechnical design, land surveying specialist teams, reinforcement detailing, in-house post-tensioning design and installation. We use the latest digital technologies to implement a state of the art digital build before any manufacture or construction commences to ensure absolute certainty during project delivery.
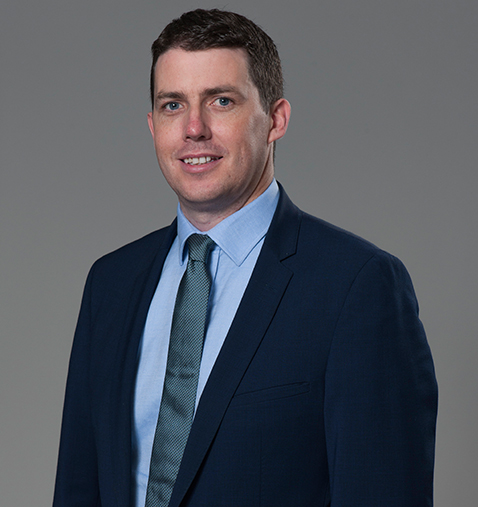
Appointed to lead Expanded’s concrete structures and geotechnical business, Peter has almost 20 years expertise, during which he has acquired an extremely broad skillset gained on a range of large scale projects such as Crossrail, London’s Leadenhall Building and most recently on Newfoundland, an iconic residential scheme on the Canary Wharf skyline.
As a qualified Civil Engineer, known for his ability to rise to complex challenges, he leads teams that focus on both learning, and delivering, efficient and innovative solutions. Known to empower and nurture talent, he fosters a culture on projects where a broad range of skills and competencies are shared, from steel frame, top-down construction, cofferdam construction and the delivery of Design for Manufacture and Assembly (DfMA) solutions in various sectors.
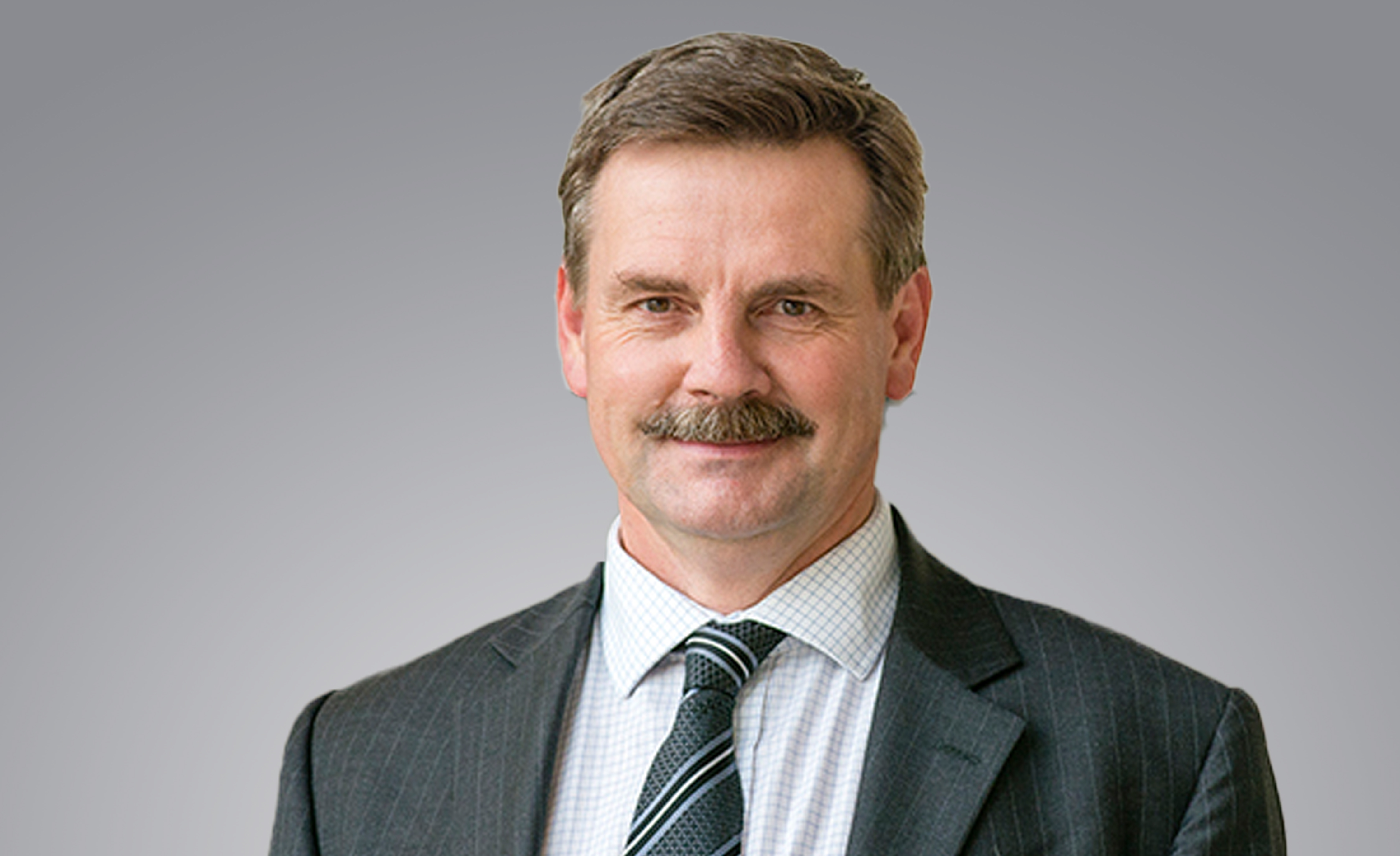
Neil Henderson started his career as a civil engineer building roads and bridges across the UK. In 1995 he joined Expanded and focused on concrete structures with a particular interest in foundations and deep basements. As a Project Manager in the London area he was responsible for a number of complex top-down basements including the apartments at One Hyde Park, the Canary Wharf Crossrail station and the new stations at Nine Elms and Battersea on the Northern Line Extension to name but a few.
Whilst his speciality is in basements he has been responsible for the civils element on the ‘Millennium Dome’, the tower blocks on One Hyde Park, the new Ascot grandstand and more recently the tunnels, track and over-ground structures on the Northern Line Extension.
As a Fellow of the Institution of Civil Engineers he is engaged in developing and training graduate engineers and is focused on developing positive and motivated teams on each of his projects. He has earned the respect of the Clients he has worked with, for delivering projects on time whilst maintaining a strong focus on safety and quality.
In his current role as one of the Operation Leaders in Expanded, Neil is responsible for managing teams on a number of live projects and is also working on tenders for future work.
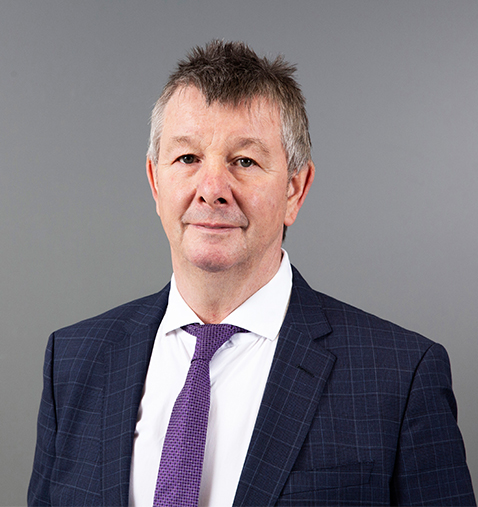
Martin has worked in the construction industry for over 30 years, delivering projects within the residential, hotel/ leisure, commercial, rail/infrastructure, mixed-use/retail and government sectors. He started his career with Laing O’Rourke Civil Engineering in 1984 as a carpenter and soon progressed through the ranks to construction manager – a role he held for 16 years, working on many of the company’s most prestigious contracts throughout the UK.
In 2002, he was promoted to Operations and Labour Relations Director. During his career, Martin has gained a wealth of knowledge in smart build techniques, including slip form and jump form core construction, bulk earthworks, basement construction (including top-down), facade retention, high- rise structures, sub and superstructure works (post-tension and traditional reinforced) and precast concrete frames.
Strongly committed to staff training and development, he mentors up and coming staff and also leads the company’s Apprentice+ scheme.
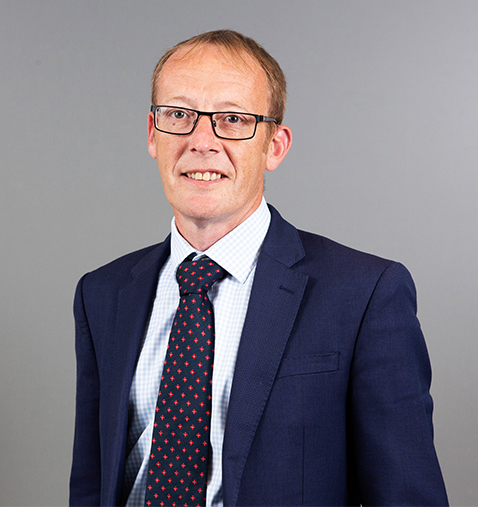
Andy is a commercial professional with over 20 years’experience in the industry. He has considerable expertise in reinforced concrete structures, gained through time spent working on site. Andy joined the business as a Quantity Surveyor and progressed to Commercial Manager and Regional Commercial Manager positions. In 2012 he transferred to the Australian business where he spent three years working on highly complex civil engineering projects before returning to the UK business in 2015 and his current role as Commercial Director for Expanded. Throughout his career, Andy has gained invaluable experience in cost control, change management and management accounts reporting.
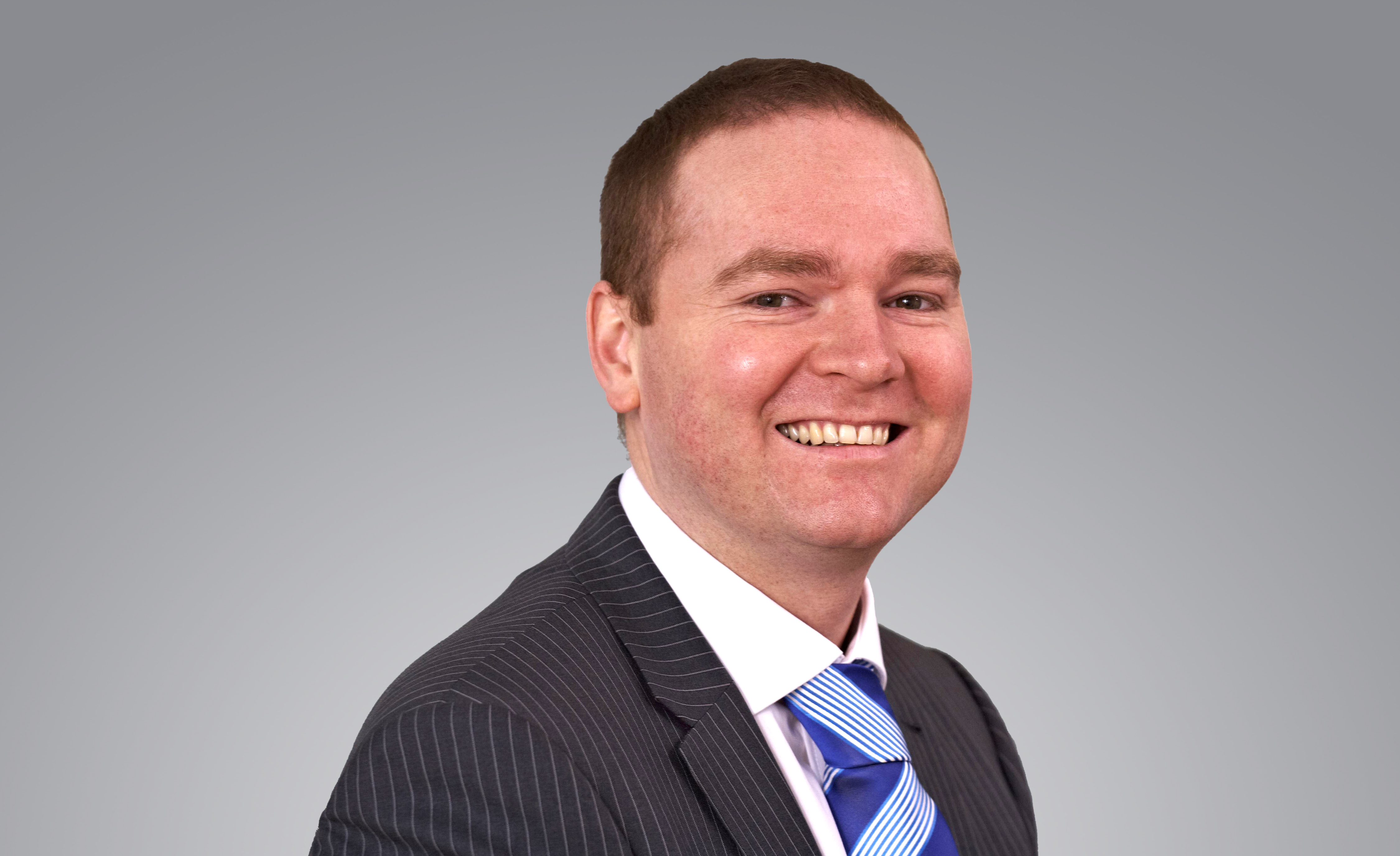
Andy is an Operations Director with over 20 years’ experience in the construction industry, specifically relating to reinforced concrete frames. Andy began his career with the business starting with O’Rourke Civil Engineering in London in 1999 and has progressed through the business fulfilling a number of varied roles. Before taking up his current role he worked extensively on a range of projects including city centre retail and commercial offices, residential towers, industrial units and high-rise construction. His particular expertise in the delivery of projects, cost control and productivity management within the RC frame section of the industry informs his ability to provide buildability and cost advice to clients and design teams. In addition to the day-to-day commercial and contractual management of RC frame projects during construction, Andy works alongside both client and design teams from very early in the process – advising on the development of cost plans, assisting in design reviews, providing advice relating to construction issues and value engineering, and ensuring that clients are provided with accurate financial advice at the outset and throughout construction.
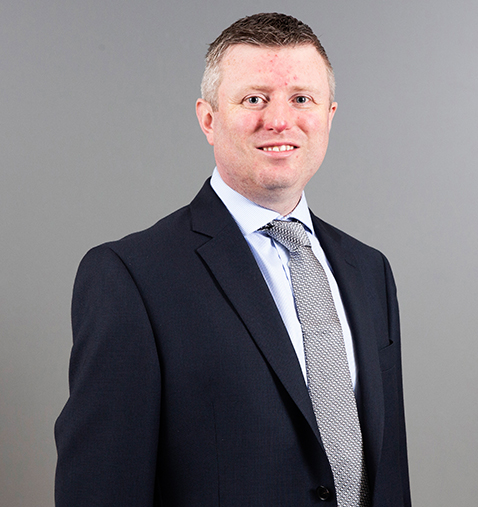
Kris joined the business in 1999, where he has gained 20 years’ experience, having been involved in a range of projects across the civil engineering, air and rail, commercial, residential and education sectors. He is thorough and committed and has worked on some of our most challenging and complex projects, particularly within tight city centre locations. Throughout this time, Kris has amassed a great deal of knowledge and experience in all stages of construction from preconstruction, delivery and post construction, delivering concrete sub and superstructure projects using in situ, precast and hybrid solutions. Kris is a proven operations manager with over 11 years’ experience in project management and operational management roles.
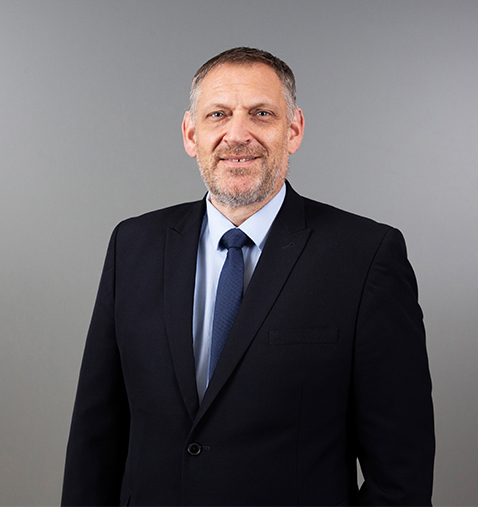
Neil joined the business in 1994 upon graduating from university and after a successful industrial placement with the company. He progressed from Site Engineer through the Engineering structure, spending a year seconded to our in house temporary works department, into project management and then into functional technical lead within the Infrastructure business, a role he held for eight years before returning to Expanded as operations manager in 2014, where he is currently responsible for delivering a £120m portfolio of contracts.
Neil brings to the role a wealth of specialist technical knowledge on deep basements and high-rise concrete frames, as well as problem-solving ability developed over 20 years within the construction industry. He is committed to progressing our engineering background and developing the 200 engineers within his function to become members of the Institution of Civil Engineers and also to identify and develop suitable undergraduates through the Laing O’Rourke scholarship scheme.
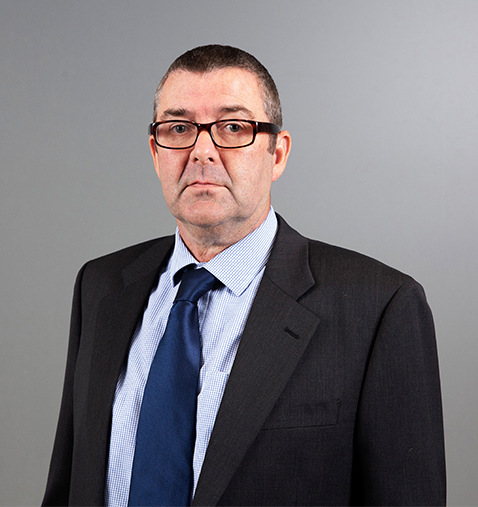
With over 30 years experience in the construction industry Mitchell has a wide range of experience through residential, hospitality, theme parks / resorts, healthcare, infrastructure and industrial. His experience in deploying and managing both directly employed and subcontracted resources coupled with high quality safe methods of construction leads to well organised motivated delivery.
Mitchell is experienced in leading pre-construction planning and services teams, cost planning and negotiating bids and final accounts. He has a wide range of experience in building methods and solutions that lead to improved safety, build programmes and costing.
Mitchell has a range of operational responsibilities across a number of projects in the UK including high rise residential, industrial, health care and highway infrastructure / bridge construction, utility infrastructure and earthworks together with business development and bidding roles.
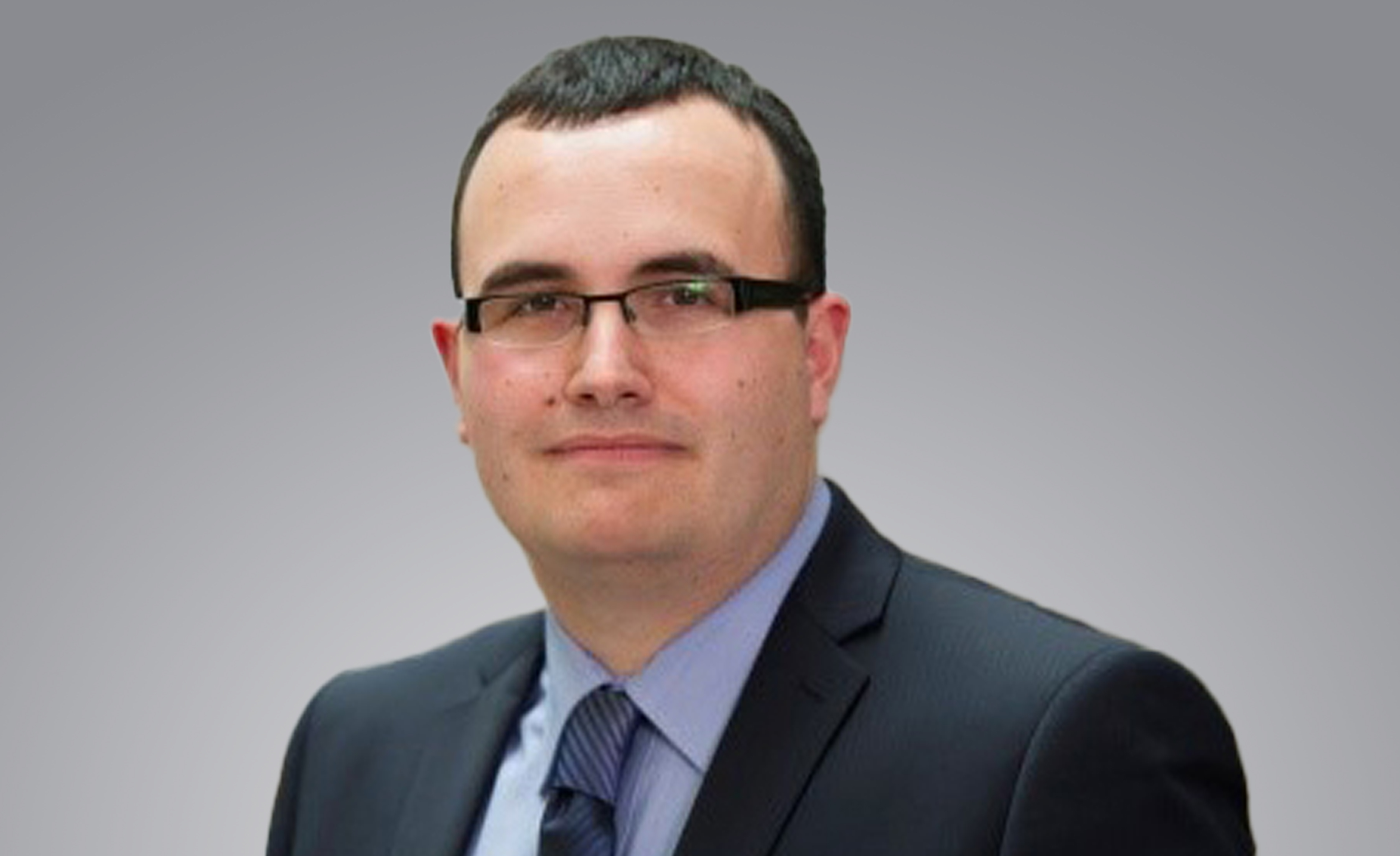
Barry leads the estimating teams across our Geotechnical, Structures, Vetter UK and Facades businesses, drawing on 16 years of varied international construction, estimating and cost planning experience. He joined the business in 2007 as an Estimating Leader on the £120m Salford and Wigan BSF programme in Manchester – the first of its kind in the UK, before becoming a member of the CIOB.
Barry spent five years working as a Senior Estimator in our Canadian team, where he established and led the estimating function for the pursuit of major projects in a range of sectors, including education and stadia.
Upon his return to the UK in 2014, he joined Expanded as Estimating Leader, where he has been a key member of the team in securing high profile, complex and challenging projects across the UK.
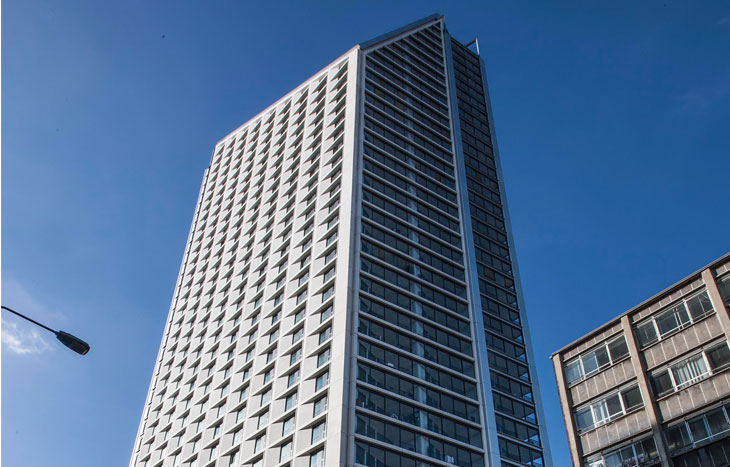
- ONE HYDE PARK
- MERANO RESIDENCE
- BRIGHTON 3Ts
- ST JAMES QUARTER
- HEATHROW TERMINAL 2
- TWO FIFTY ONE, SOUTHWARK
- CLARGES
- SOUTHBANK PLACE
- WOOD WHARF H1-H4 CLADDING
- WOOD WHARF D1/D2 CLADDING
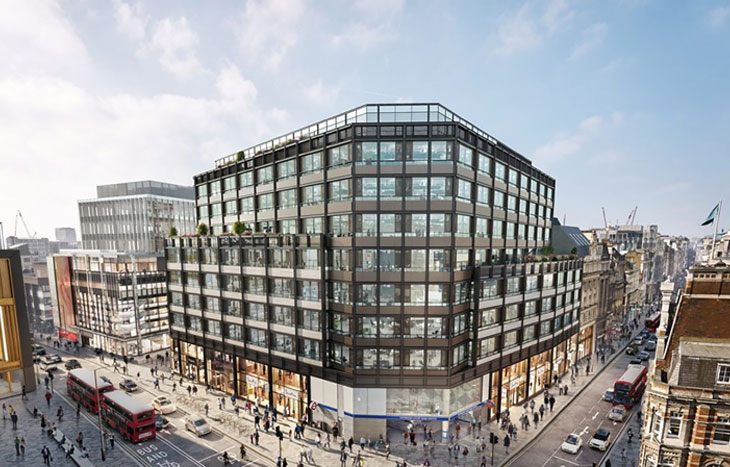
- THE EITIHAD STADIUM
- HOUGH END LEISURE CENTRE
- LEVENHULME LEISURE CENTRE
- THE FACTORY
- MANCHESTER INSTITUTE FOR HEALTH AND PERFORMANCE
- SOHO PLACE (1 OXFORD STREET)
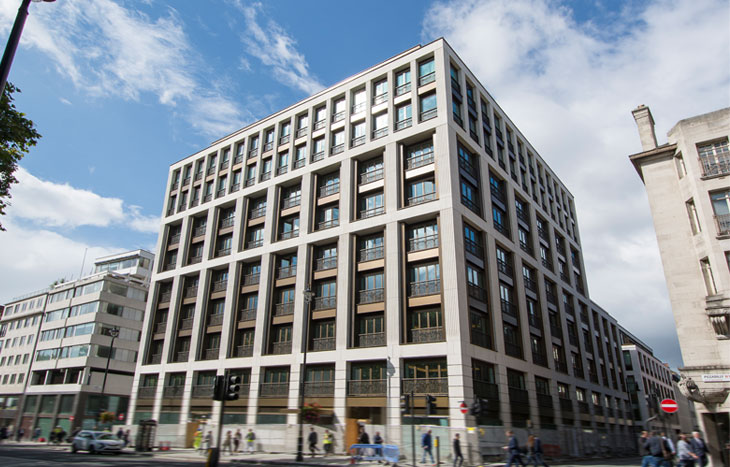
- SOUTH QUAY PLAZA
- ONE BLACKFRIARS PHASE 2
- WOOD WHARF BASEMENT
- NINE ELMS SQUARE
- CLARGES
- ONE HYDE PARK
- THE ATRIUM
- SOUTHBANK PLACE
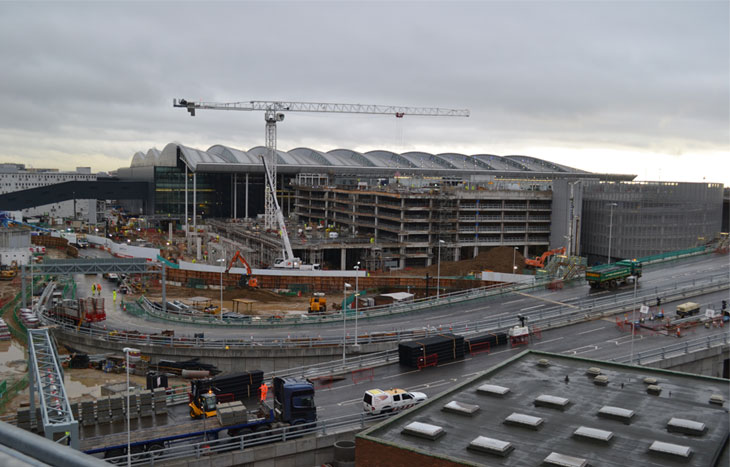
- PENWHAPPLE RESERVOIR
- LOCH ARKLETT RESERVOIR
- CANARY WHARF STATION BOX
- HEATHROW TERMINAL 2
- DALBEATTIE
- HEATHROW TERMINAL 2 MSCP EAST
- CRAIGNURE
- BOAT OF GARTEN
- HS2 ENABLING WORKS
- MANCHESTER AIRPORT TRANSFORMATION
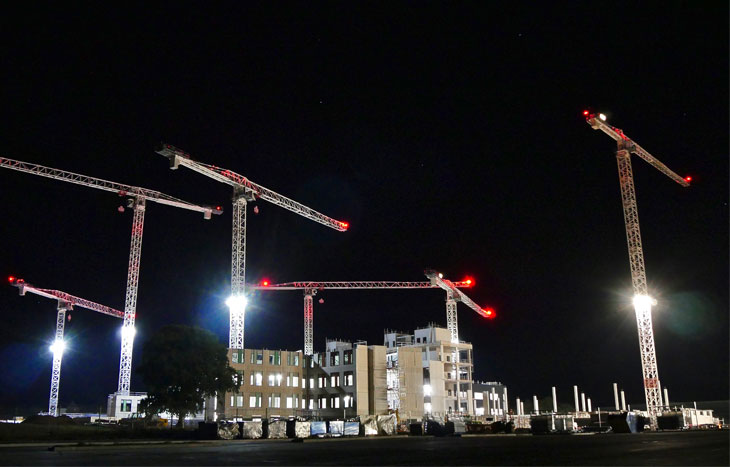
- FARNHAM ROAD HOSPITAL
- GUY'S AND ST. THOMAS' HOSPITAL
- CLATTERBRIDGE CANCER CENTRE
- DUMFRIES & GALLOWAY ROYAL INFIRMARY
- WEST CUMBERLAND HOSITAL
- GRANGE UNIVERSITY HOSPITAL
- BRIGHTON 3Ts
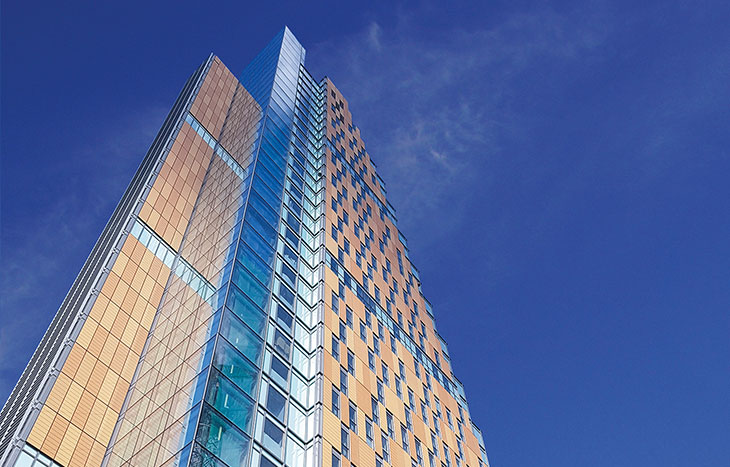
- IMPERIAL WEST BLOCK F
- GRAPHENE ENGINEERING INNOVATION CENTRE 2
- HENRY ROYCE INSTITUTE
- YORKSHIRE PRIORITY SCHOOLS
- BLAVATNIK SCHOOL OF GOVERNMENT
- OXFORD BIOCHEMISTRY PHASE 2
- MANCHESTER UNIVERSITY ENGINEERING CAMPUS
- BELLATRIX (BIOMEDICAL RESEARCH FACILITY)
- OXFORD BEECROFT BUILDING
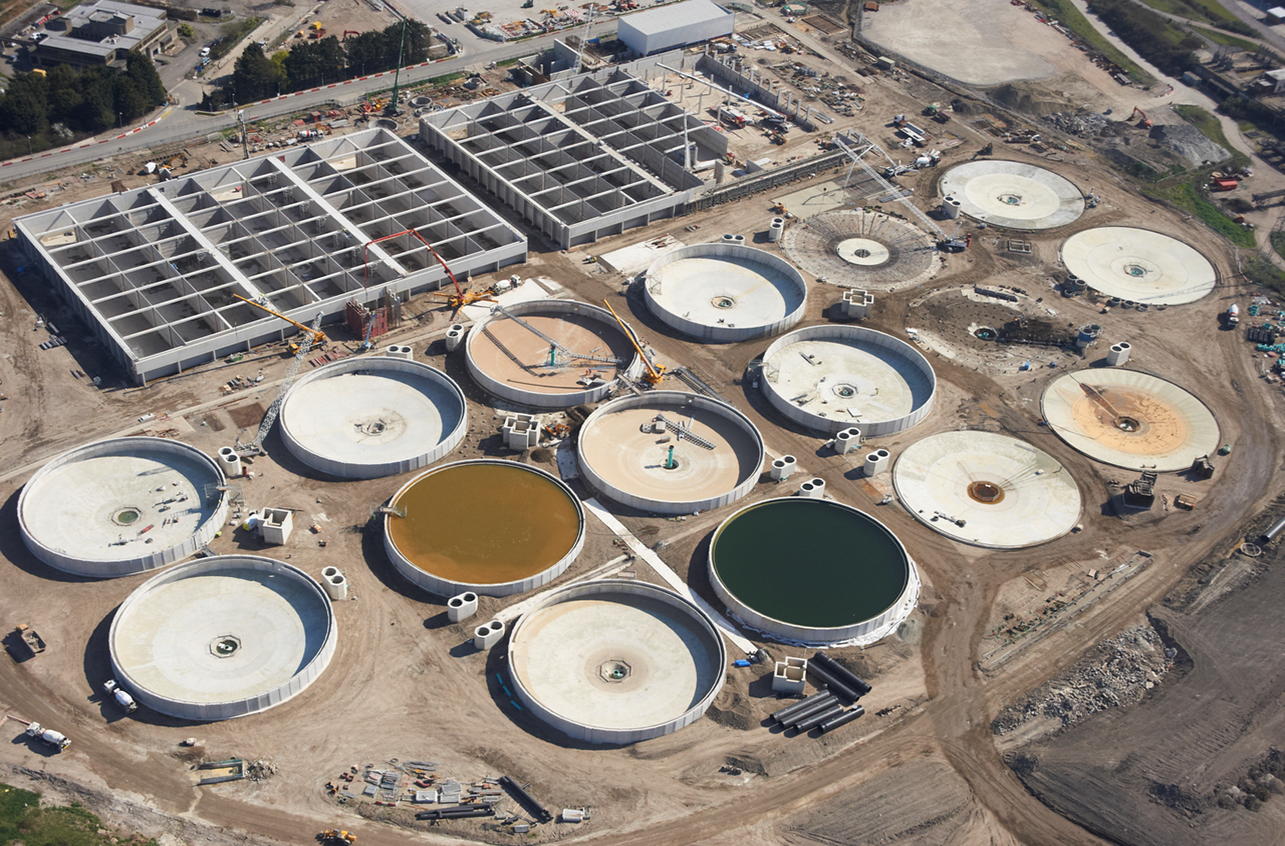
- HATHERSHAW
- DAVYHULME WASTEWATER TREATMENT WORKS
- BLACKBURN WTW
- BECKTON STW AMP7 UPGRADE
- TIDEWAY - ALBERT EMBANKMENT
- TIDEWAY - FALCONBROOK PUMPING STATION
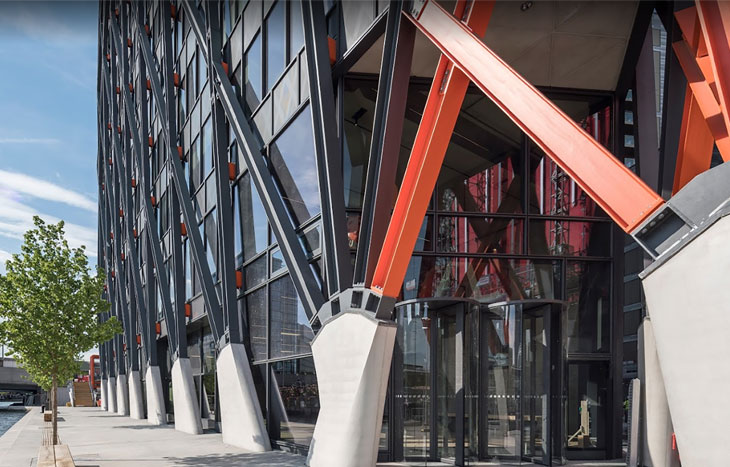
- THE LEADENHALL BUILDING
- 55-65 NORTH WHARF ROAD
- NO. 2 ST. PETER’S SQUARE
- LD7 DATA CENTRE
- SCOTTISH POWER HQ
- BBC PLOT A
- GOOGLE PRECAST
- JAGUAR LAND ROVER - TRIANGLE BUILDING
- JAGUAR LAND ROVER - NOISE VIBRATION & HARSHNESS (NVH)
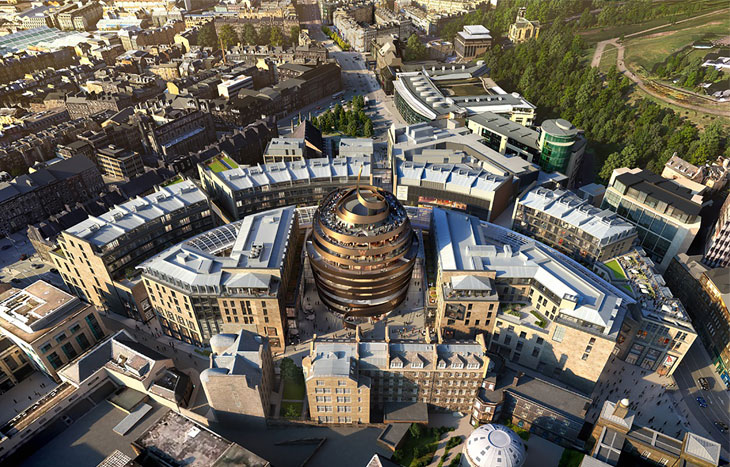
- 21-32 NEW OXFORD STREET
- WATFORD CHARTER PLACE
- WESTGATE OXFORD
- EDINBURGH ST JAMES
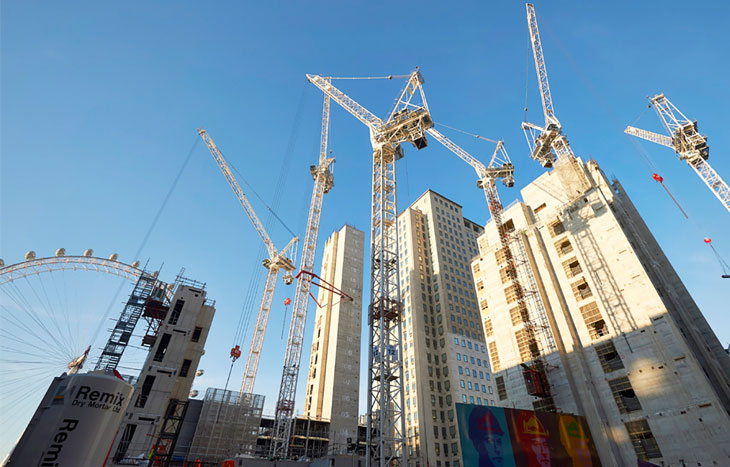
- 250 CITY ROAD
- SOUTHBANK PLACE
- TWO FIFTY ONE, SOUTHWARK
- NEWFOUNDLAND
- SOUTH QUAY PLAZA
- WOOD WHARF BLOCK A1/ ONE PARK DRIVE
- ONE BISHOPSGATE PLAZA
- 190 STRAND
- X1 MEDIA CITY
- ONE HYDE PARK
- ONE ELEPHANT ROAD
- HINKLEY WORKERS CAMPUS
We completed the piling, sub and superstructure for this mixed-use development in Islington, London. Substructure works included the demolition of the existing basement and construction of an insitu reinforced concrete single and double-storey basement. Superstructure works included construction of a 42-storey tower and five eight-storey blocks. The tower was constructed using a jumpform core, while the remaining eight-storey blocks comprise a precast solution. Using our in- house expertise, we could convert the original core designs to the five eight-storey blocks into twinwall (over 10,000m2); insitu slabs generally converted to lattice slabs (66,000m2 floor area); and Stairmaster stairs converted to precast.
Re-development of Shell Centre adjacent, to London eye. Construction of three-storey basements and eight towers ranging in height between 10 and 40 storeys. Four of the towers were fully acoustically isolated. The structures are made up of a combination of in-situ reinforced concrete, post tension, reinforced concrete DfMA elements and structural steel. The high-rise concrete cores were slipformed with lower-rise being constructed with off-site manufactured twinwall. Expanded works included the supply and install of cladding for 30-storey residential structure, featuring the first pre-stressed concrete cladding panels to be manufactured in the UK.
Two Fifty One comprises a 41-storey residential tower – 70% of which was constructed off site using DfMA. A 33% reduction of the frame assembly programme was secured using DfMA rather than in situ methods for the residential tower. In addition, the DfMA approach provided increased certainty of time and labour costs, increased productivity, reduced onsite activities and an opportunity to ‘design out’ significant health and safety risks. This unrivalled certainty was made possible through early client engagement and the close links between our planners, designers and in- house manufacturing facilities. The project met the Passive Home Standards and Code for Sustainable Homes Level 3.
We delivered the substructure, frame and core for this 60-storey residential tower in Canary Wharf. The structural frame solution consists of an exoskeleton steel structure with node floors every four floors. The jumpform structural core is a combination of precast and post-tensioned / in situ concrete floors. A bespoke dual jumpform system was designed and built in collaboration with PERI, reducing the floor cycle from 5.5 to 4.4 days. Expanded engineers designed a bespoke piece of temporary works to enable the use of the lift shaft for passenger hoists, which enabled the lift contractors to undertake works while the hoist was used on the levels above.
We formed the two-levels of basement via top-down sequence to allow the core construction to begin for the 68-storey building. An optimised jumpform system formed the main core, with post-tensioned slabs and high-strength columns. One of 30 pours in total, the final 1,200m3 pour for the 3m deep raft slab was a significant milestone for the project. The pour was completed with only two mobile concrete pumps, peaking at 180m3 /hour. Precast, double-storey columns form the perimeter vertical elements, with twinwall dividing the core into separate lift shafts. Precast stairs and landings have been installed through the jumpform system.
We are constructing this 57-storey tower (A1) and double-level basement and site-wide basement raft slabs shared by A1 and two other buildings (A2 and A3) for Canary Wharf Contractors Ltd. Our scope includes temporary works propping to the combi-wall, pile trimming, pile caps and raft slab construction. It also includes drainage, retaining walls and substructure construction to B2 level, ground floor slab to building A1 and superstructure floor slab and core construction from basement to roof. Precast stairs installation and tower cranes bases construction for buildings A1, A2 and A3 also form part of the scope.
We delivered the substructure and superstructure for this 42-storey tower in the City of London. The tower comprises a central core surrounded by a 1050m2 floor plate which tiered inwards as the structure rose in height. The floor slabs took on a complex geometric form with the presence of three column-free sharp angled corners. Pre-fabricated reinforcement mesh was integrated into the design of the post tensioning, supplemented by double-height precast concrete columns. The central core was constructed using a jumpform system with GRP shuttering used within the cells for forming doorways – minimising the requirement for striking or re-use of timber.
We designed and constructed the sub and superstructure for this luxury residential development in central London. Our works included the construction of a secant wall around and through an existing three-level basement. Innovative temporary works allowed demolition of the existing basement, allowing construction of a new four-level basement. The new basement build utilised precast concrete solutions to construct six lift and stair cores, whilst also saving 30 weeks’ work. The superstructure frames range in height from five to eight-storeys and were constructed using precast solutions, creating the 206 apartments. A two level basement and a seven-storey superstructure was also constructed on a neighbouring island.
We delivered the first phase of the new luxury residential development at Salford Quays. Phase One of the development delivered 275 apartments. We completed pile cap excavation with concrete basement and superstructure construction, including a 27-storey slipformed core and post-tensioned upper floors. Our works included bulk excavation and piling mat works, excavation and formation of the reinforced concrete works including; pile caps, ground beams, concrete bases, ramps basement sumps and lift pits, basement shear walls and columns and construction of the ground floor slab, podium slab, ground and upper floor shear walls and columns, post tensioned floor slabs, precast concrete staircases and insitu concrete floor slab.
One Hyde Park consists of 85 luxurious apartments ranging in size from 1,000 square feet to over 27,000 square feet and is set in the heart of Knightsbridge. The four pavilions display white precast columns and spandrel beams which form the external structural frame. The core frame consists of a reinforced concrete structural steel composite solution with post tensioned reinforced concrete slabs. For cladding and glazing to fit the double height external precast had to be installed to within 4mm’s. The basement of the structure was constructed top down at the same time as the superstructure.
Tribeca Square (Elephant 1) was completed by Laing O’Rourke in 2017 and is a mixed-use development comprising of 24, 19 and 16 storey towers with two basement levels which offer parking space and accommodate plant rooms. Self-delivery ensured that the construction, design and off-site manufacturing teams adopted full efficiency with the utilisation of precast elements and pre-fabricated bathroom pods and smartwall. Our DfMA approach allowed for a 32% reduction in programme duration and a 29% labour saving. The use of Digital Engineering helped us to create a multidimensional model that helped visualise the project showing which components were needed and where.
Using the latest offsite construction practices under an NEC contract, Expanded supported Laing O’Rourke in delivering modular accommodation blocks across two locations, one in Bridgwater and another closer to the Hinkley project, all in less than 14 months on site. A 30% programme saving compared to traditional methods was secured using our efficient DfMA approach. Due to one campus being located close to a housing estate, minimising disruption was essential. Residents highlighted that noise generated by piling works was a concern, so we used a smaller piling rig to reduce it. Monthly meetings with residents and stakeholders were continued throughout the works to establish close ties with the community.
Expanded delivered top-down construction of a three-storey basement across the footprint of the site, followed by four individual superstructures. These comprised ten and five-storey residential reinforced concrete structures, made up of precast columns, twin-wall cores and lattice plank with in-situ concrete topping floors; seven and four storey steel structures, both with a solid precast concrete core and MEGAPLANK floors which only required in-situ stitch reinforcement. The basement two slab was constructed just below the ground floor slab, tied to the ground floor slab and then lowered into position via hydraulic strand jacks following completion of the basement excavation.
Two Fifty One comprises a 41-storey residential tower – 70% of which was constructed off site using DfMA. A 33% reduction of the frame assembly programme was secured using DfMA rather than in situ methods for the residential tower. In addition, the DfMA approach provided increased certainty of time and labour costs, increased productivity, reduced onsite activities and an opportunity to ‘design out’ significant health and safety risks. This unrivalled certainty was made possible through early client engagement and the close links between our planners, designers and in- house manufacturing facilities. The project met the Passive Home Standards and Code for Sustainable Homes Level 3.
We were appointed to construct a new two-level basement box, which comprises a car park and health suite, connects all six high rise blocks, filling the entire site footprint. We constructed the six reinforced concrete frames delivering 800+ apartments(including two penthouse levels). All six high rise blocks have PCC edge beams and twin wall to cores and central shear walls provided by Explore Manufacturing along with PCO stairs/landings provided by Bison. In addition to this each high rise has extensive architectural steel with coloured steel balconies to all even levels and double height vertical and diagonal bracing.
We delivered the substructure, frame and core for this 60-storey residential tower in Canary Wharf. The structural frame solution consists of an exoskeleton steel structure with node floors every four floors. The jumpform structural core is a combination of precast and post-tensioned / in situ concrete floors. A bespoke dual jumpform system was designed and built in collaboration with PERI, reducing the floor cycle from 5.5 to 4.4 days. Expanded engineers designed a bespoke piece of temporary works to enable the use of the lift shaft for passenger hoists, which enabled the lift contractors to undertake works while the hoist was used on the levels above
We delivered the piling, tower cranes, substructure and superstructure works as part of the redevelopment of the 27-storey Shell Centre tower. Our works included construction of a three-level concrete basement substructure for one third of the site footprint, a two-level basement for the remainder of the site footprint and construction of eight new buildings ranging between 11 and 37 storeys. Overall 120,000m3 of concrete was required and 237,600m2 floor area were constructed using a combination of insitu, precast, post-tensioning, metal decking and slipform cores. Five buildings are separated from their foundations by acoustic bearings to avoid vibration from underground lines.
We completed the piling, sub and superstructure for this mixed-use development in Islington, London. Substructure works included the demolition of the existing basement and construction of an insitu reinforced concrete single and double-storey basement. Superstructure works included construction of a 42-storey tower and five eight-storey blocks. The tower was constructed using a jumpform core, while the remaining eight-storey blocks comprise a precast solution. Using our inhouse expertise, we could convert the original core designs to the five eight-storey blocks into twinwall (over 10,000m2); insitu slabs generally converted to lattice slabs (66,000m2 floor area); and Stairmaster stairs converted to precast.
Expanded constructed the reinforced concrete frame for this high-end residential and commercial property, comprising of 28-storeys with a 3-level basement. Top down construction was used to construct the basement using permanent and temporary plunge columns, along with a secant wall and bearing piles. The superstructure was constructed using lattice and twin wall. The basements were formed using traditional in-situ concrete methods. Expanded successfully dealt with the logistical challenges and space constraints within this site, situated just South of the River Thames and worked closely with the sister business Select Plant Hire in management of the tower cranes on site.
We formed the two-levels of basement via top-down sequence to allow the core construction to begin for the 68-storey building. An optimised jumpform system formed the main core, with post-tensioned slabs and high-strength columns. One of 30 pours in total, the final 1,200m3 pour for the 3m deep raft slab was a significant milestone for the project. The pour was completed with only two mobile concrete pumps, peaking at 180m3 /hour. Precast, double-storey columns form the perimeter vertical elements, with twinwall dividing the core into separate lift shafts. Precast stairs and landings have been installed through the jumpform system.
We completed the piling,substructure and construction of a complex three storey basement. The substructure is enclosed by a 300m-long secant wall constructed of 400 piles, the basement is founded on 140 bearing piles. Construction of level B3 involved installing a 3m deep raft foundation using a single concrete pour of 3,300m3. Precast panels were then used to form passenger/vehicle lift cores up to ground level to access the hotel. Infill floor areas were completed using reinforced concrete slabs. The concrete raft pour was delivered a week ahead of schedule. The pour took only 24 hours to complete with two teams working in shifts.
We are constructing this 57-storey tower (A1) and double-level basement and site-wide basement raft slabs shared by A1 and two other buildings (A2 and A3) for Canary Wharf Contractors Ltd. Our scope includes temporary works propping to the combi-wall, pile trimming, pile caps and raft slab construction. It also includes drainage, retaining walls and substructure construction to B2 level, ground floor slab to building A1 and superstructure floor slab and core construction from basement to roof. Precast stairs installation and tower cranes bases construction for buildings A1, A2 and A3 also form part of the scope.
Expanded delivered an enabling works package for R&F Properties in Vauxhall, London. The ten-acre site will offer over 1,800 new homes as part of a residential led mixed-use scheme comprising a total of 12 buildings, including a trio of slender towers rising to 54 storeys. Expanded delivered these works nine weeks early. Key success factors included identifying programme opportunities (such as driving workforce productivity through forming good relationships with the team), and holding milestone celebrations and daily activity briefings with supervisors to ensure productivity and progress was encouraged and maintained.
Expanded delivered top-down construction of a three-storey basement across the footprint of the site, followed by four individual superstructures. These comprised ten and five-storey residential reinforced concrete structures, made up of precast columns, twin-wall cores and lattice plank with in-situ concrete topping floors; seven and four storey steel structures, both with a solid precast concrete core and MEGAPLANK floors which only required in-situ stitch reinforcement. The basement two slab was constructed just below the ground floor slab, tied to the ground floor slab and then lowered into position via hydraulic strand jacks following completion of the basement excavation.
One Hyde Park consists of 85 luxurious apartments ranging in size from 1,000 square feet to over 27,000 square feet and is set in the heart of Knightsbridge. The four pavilions display white precast columns and spandrel beams which from the external structural frame. The core frame consists of a reinforced concrete structural steel composite solution with post tensioned reinforced concrete slabs. For cladding and glazing to fit the double height external precast had to be installed to within 4mm’s. The basement of the structure was constructed top down at the same time as the superstructure.
Situated on a seven-acre site, this mixed-use scheme has transformed Camberley town centre into a vibrant, highly accessible location. The development comprises 218 residential units (55 of which are affordable and provide key worker accommodation), together with restaurants, cafés and bars, 17 retail units, a nine-screen multiplex cinema, bowling, a health and fitness club and a 300-space multi-storey car park. We also provided a further 383 car parking spaces. Expanded successfully delivered the structural elements for this mixed-use retail complex – with commercial, leisure, private and social housing, as well as extensive highway and public realm works.
Re-development of Shell Centre adjacent, to London eye. Construction of three-storey basements and eight towers ranging in height between 10 and 40 storeys. Four of the towers were fully acoustically isolated. The structures are made up of a combination of in-situ reinforced concrete, post tension, reinforced concrete DfMA elements and structural steel. The high-rise concrete cores were slipformed with lower-rise being constructed with off-site manufactured twinwall. Expanded works included the supply and install of cladding for 30-storey residential structure, featuring the first pre-stressed concrete cladding panels to be manufactured in the UK.
One Hyde Park consists of 85 luxurious apartments ranging in size from 1,000 square feet to over 27,000 square feet and is set in the heart of Knightsbridge. The four pavilions display white precast columns and spandrel beams which from the external structural frame. The core frame consists of a reinforced concrete structural steel composite solution with post tensioned reinforced concrete slabs. For cladding and glazing to fit the double height external precast had to be installed to within 4mm’s. The basement of the structure was constructed top down at the same time as the superstructure.
Expanded constructed the reinforced concrete frame for this high-end residential and commercial property, comprising of 28-storeys with a 3-level basement. Top down construction was used to construct the basement using permanent and temporary plunge columns, along with a secant wall and bearing piles. The superstructure was constructed using lattice and twin wall. The basements were formed using traditional in-situ concrete methods. Expanded successfully dealt with the logistical challenges and space constraints within this site, situated just South of the River Thames and worked closely with the sister business Select Plant Hire in management of the tower cranes on site.
Expanded have constructed the first new development at Brighton 3T’s (Teaching, Trauma and Tertiary Care Centre). The project has utilised a significant amount of manufactured concrete components from the sister business Explore Manufacturing. Using a team that understand DfMA delivery, they have constructed the two-storey basement and thirteen floors over three wings in over a year. Expanded have also installed 1600 pre-cast concrete cladding components. The Expanded team worked closely with the wider Laing O’Rourke business and sister companies to ensure that the live hospital continues to function throughout the construction work and with minimal disruption to the patients.
A 1.7millionft2 mixed-use development in the centre of Edinburgh, replacing the existing St James Centre with 850,000ft2 of retail, leisure and hotel facilities and 152 new homes. Our Engineering Excellence Group have provided technical advice to de-risk delivery of this major project. Our input introduced a DfMA approach to deliver the extensive subterranean car park and feature stone clad facades, delivering over 4,000 components. The extensive basement was engineered to remove intrusive props through rock anchoring and a progressive excavation sequence. We have also utilised 4D modelling to plan and validate the complex underpinning works to the John Lewis store.
Expanded constructed the 90,000m3 reinforced concrete raft slab to support the Terminal steel frame. The raft slab construction required extensive de-watering for the duration of the works. Meticulous waterproofing installation was required to avoid water ingress which could affect the baggage-handling plant at one of the busiest airports in the world. Works also included construction of the new cooling station which was clad in black and white reinforced concrete precast panels.
Two Fifty One comprises a 41-storey residential tower – 70% of which was constructed off site using DfMA. A 33% reduction of the frame assembly programme was secured using DfMA rather than in situ methods for the residential tower. In addition, the DfMA approach provided increased certainty of time and labour costs, increased productivity, reduced onsite activities and an opportunity to ‘design out’ significant health and safety risks. This unrivalled certainty was made possible through early client engagement and the close links between our planners, designers and in- house manufacturing facilities. The project met the Passive Home Standards and Code for Sustainable Homes Level 3.
Expanded delivered top-down construction of a three-storey basement across the footprint of the site, followed by four individual superstructures. These comprised ten and five-storey residential reinforced concrete structures, made up of precast columns, twin-wall cores and lattice plank with in-situ concrete topping floors; seven and four storey steel structures, both with a solid precast concrete core and MEGAPLANK floors which only required in-situ stitch reinforcement. The basement two slab was constructed just below the ground floor slab, tied to the ground floor slab and then lowered into position via hydraulic strand jacks following completion of the basement excavation.
Re-development of Shell Centre adjacent, to London eye. Construction of three-storey basements and eight towers ranging in height between 10 and 40 storeys. Four of the towers were fully acoustically isolated. The structures are made up of a combination of in-situ reinforced concrete, post tension, reinforced concrete DfMA elements and structural steel. The high-rise concrete cores were slipformed with lower-rise being constructed with off-site manufactured twinwall. Expanded works included the supply and install of cladding for 30-storey residential structure, featuring the first pre-stressed concrete cladding panels to be manufactured in the UK.
Expanded are supplying and installing precast façade elements for this new development in Canary Wharf
Expanded are supplying and installing precast façade elements for this new development in Canary Wharf
Expanded was contracted to increase stadium capacity from 48,000 to 55,000 and increase the range of facilities for visitors. We engaged with MCFC to develop a logistics strategy that limited disturbance to the stadium operation, using 3D modelling to analyse risk and disruption. The construction of the upper tier required new columns to run through the existing structure and concourse areas. The location of these columns was balanced against the size of plant required to sink the foundation piles. We worked closely with the client and design team, using the same columns to provide temporary support for the existing roof.
Hough End Leisure Centre was part of a major programme of investment undertaken by Manchester City Council that created three new leisure centres – all built by Expanded. Among other facilities, the building includes a 25m six-lane swimming pool, a 17m learner pool, a gym with 90 stations and two squash courts. The first floor ‒ above a brick-clad ground level ‒ was conceived as a lightweight metal and glass ‘pod’ with bronze-toned rainscreen cladding. To highlight any concerns between information sources, the swimming pool pipes and joints for concrete pours that have water bar embedded into them were digitally modelled.
Working in a collaborative partnership to Manchester City Council, we developed a set of standardised components to be used on this project and any future leisure centres in the area. This improved efficiency across initial investment and operational costs. The leisure centre includes a 25m main pool. A 12-person sauna and steam rooms is easily accessible from the adjacent changing rooms. First-floor facilities include a 264m2 health and fitness suite, equipped with 60 stations, and an adjoining 100m2 space that can host community meetings and serve as a dance studio for 30 people.
Expanded is a construction partner for two-stage design-and-build project for a 16,000m2 performing arts venue in Manchester city centre. The building will serve as a permanent home for Manchester International Festival, with a combined capacity of up to 6,500. The Factory is a challenging construction project, most notably in the complexity of the structural proposals, the constrained site, interface with heritage structures, and the exacting performance requirements. Having reviewed the early and emerging design reports, we carried out in-depth option appraisals to determine how we would construct The Factory, identifying opportunities to improve programme or reduce cost.
MIHP’s state-of-the-art health, performance and research facilities include a range of cutting-edge technology and facilities. The concrete-framed health/office block is clad in off-white concrete panels, with glazing which includes ceramic-backed glass spandrels and glazed-in anodised infill panels. The steel-framed performance analysis hall has half-round aluminium cladding above an engineering brick plinth. We used DfMA for the concrete frame and external off- white concrete panels. This reduced activities and labour on site, and thereby noise and disturbance to neighbours whilst providing a high quality off site manufactured structure/elements. This method of construction is more sustainable as it reduces waste, and has less CO2 emissions from deliveries.
Situated directly above Tottenham Court Road station, the Soho Place development presents numerous technical challenges due to its central location, stringent acoustic requirements and glass-clad beacon design. When complete, the 285,000ft2 mixed-use, two-building scheme will comprise 209,000ft2 of offices, 36,000ft2 of retail space, a 40,000ft2 theatre and a new public realm. The unique design is configured as a tiered stack of volumes, which not only work around the rail infrastructure beneath, but also relate to the scale of the internal five- storey 350-seat theatre.
Penwhapple Reservoir is located approximately 8km West of Girvan, South Ayrshire. The project was the first of its kind for Scottish Water, using a DfMA solution for construction of a new spillway, measuring 100 metres in length with a 3-metre base and 2.5-metre height. This was formed using pre-cast concrete base units with twinwall. Expanded oversaw pipework diversions, construction of a new vehicle access bridge, re-routing of existing services and temporary works including existing dam retention and slope formation. Expanded also oversaw the rock anchoring works, carried out by others.
Laing O’Rourke designed and installed 64 rock anchors from dam crest through the body of the structure to an underlying rock formation with the depths varying from 25m to 52m. Replacement of a one span, over-flow Bridge and repairs to abutments were made. Repairs were also carried out on downstream masonry facing blocks between valve houses. This process of drilling into the Dam structure is the biggest that has been attempted in the UK, with the Anchor stressing the biggest in Europe. The work is being completed by Laing O’Rourke sub-contractor BAM Richie.
Expanded Structures and Expanded Geotechnical combined on the innovative delivery of a station box measuring 250 metres by 30 metres wide, in a water-filled dock, 10 metres deep. The completed project was then incorporated into a six-storey development with retail, restaurants and a community facility beneath a rooftop garden. Expanded Piling used a range of techniques to ensure for a safe and efficient station box construction. The cofferdam was built with noise and vibration levels at a minimum, reducing any potential disruption to nearby workers and residents. Expanded Piling received an award from Ground Engineering in 2014, for technical design and delivery on this project.
Expanded constructed the 90,000m3 reinforced concrete raft slab to support the Terminal steel frame. The raft slab construction required extensive de-watering for the duration of the works. Meticulous waterproofing installation was required to avoid water ingress which could affect the baggage-handling plant at one of the busiest airports in the world. Works also included construction of the new cooling station which was clad in black and white reinforced concrete precast panels.
Dalbeattie was a failing sewage treatment works that required immediate remedial action throughout the site. Our scope included the provision of two new bio-filters, refurbishment of two PSTs and two HSTs, new sludge pump station and recirculation station, new outlet and new inlet works. In terms of innovation, the new bio-filter tanks make use of precast concrete wall panels. Square distribution chambers were also changed to precast concrete manhole rings for speed of construction, to reduce working time for men in excavations and to benefit from the quality of offsite manufactured products.
The MSCP East Project forms part of the Eastern Campus development programme at Heathrow Airport, including construction of a new multi storey car park providing 1,380 spaces. Access to the car park is via new road infrastructure and reinforced concrete ramps spanning over a new Terminal 3 approach road. As part of the MSCP East project the car park ties into the new Terminal 2A building via a covered court and link bridges at both high and low level.
The Craignure project on the Isle of Mull for the client, Scottish Water. Work involved the construction of a new service reservoir, the upgrade of service pumps, and a new tanker delivery pump station. Additionally, there was work to upsize the raw water main to increase the output from the Tobermory Water Treatment.
Expanded constructed a combined sewer overflow, a control building, an intermediate pumping station and four septic tanks. Additionally, Expanded upgraded the main town sewer, relieving flooding issues within the town and reducing contamination risk. Temporary works included a sheet piled cofferdam, a thrust wall, piling mats, excavation support, sewer diversion and a de-watering system. DfMA was used to construct the main structures, including a permanent shutter to save time and cost, and precast concrete with mechanical equipment pre- installed. As the project was in the Cairngorm National Park, additional environmental protection was required to ensure no environmental damage occurred during construction.
Expanded are working under the Laing O’Rouke / Murphy joint venture to deliver the enabling works within the BIS Triangle. These works will allow for the re-direction of traffic within this area through the creation of four new bridges, which cross the M42, A453 and A446.
Laing O’Rourke was the Principal Contractor for the design and build of Package 01 of the Manchester Airport Transformation Programme. Our scope of works included a new extension to the existing Terminal 2, piers, outbound baggage hall and a new 3,700-space multi-storey car park, with phased handover of facilities between 2019 and 2021. The programme includes expansion of Terminal 2 by 140% through extension and space reconfiguration, as well as provision of new grade and multi-storey car parks and surrounding infrastructure. In conjunction with Explore Manufacturing, Expanded also successfully built a new car park for T2, predominantly of DfMA construction.
Completed in 2015, Farnham Road Hospital has a gross floor area of 6,350m2 and comprises 60-bedrooms for mental health care and is linked to an existing heritage building. Expanded were able to offer the Client the latest technology and products, such as the fully serviced internal partitioning system SmartWall, pre-cast concrete columns and lattice slabs. We delivered this project with our other integrated delivery businesses within the Laing O’Rourke group. A federated BIM model was adopted to co-ordinate the architectural design, services integration and structural strategy.
Guy’s Hospital is one of the new cancer treatment centres, built as part Government’s Cancer Reform Strategy to deliver an integrated cancer centre for patients across southeast London and beyond, combining first-class clinical care with ground-breaking research. The building’s footprint stretches over 27,000m2 over 14-storeys tall. The design achieves BREEAM Excellent status. Driving efficiency, we adopted lean manufacturing techniques. The centre’s superstructure is predominantly precast and was manufactured in our industry-leading facilities at Explore Manufacturing. Modular risers and plantrooms have also been designed by our in-house specialist; CHt to allow the efficient offsite preassembly and simple installation of M&E components.
Expanded delivered the structural frame for the Clatterbridge Cancer Centre which is formed of 11-storeys and covers 28,000m2 of area, allowing for 110 beds. The building was extended to 11 storeys after tender stage, and we worked with the design team to re-engineer this. Our Digital Engineering capabilities allowed us to represent this visually to the full range of stakeholders. Use of DfMA techniques contributed to alleviating what was already a complex logistics scheme, given the small storage space provided on site. 70% of the workforce on the project comprised of local employment. In addition, 50 apprenticeships were provided during construction.
Expanded completed the reinforced concrete structural and facade works for the 63000m2 hospital. Many of our construction solutions were a development from previous hospital projects – for example, we could increase repetition within the envelope design without compromising the aesthetic, with Explore Manufacturing able to produce 1,005 composite facade panels using just 27 typologies. Digital Engineering, innovation and offsite manufacturing helped to deliver this new hospital five months quicker than could be achieved with traditional methods.
As design-and-build contractor for this acute hospital, we delivered 19,500m2 of new-build wards and completed the refurbishment of 21,300m2 of existing wards. Our DfMA approach provided greater control over quality and allowed works to remain on programme despite some challenging weather conditions. A key constraint was the need to redevelop the hospital within the footprint of the existing buildings and clearing areas of the existing site to make way for new buildings while keeping other parts of the hospital running. Our DfMA approach provided greater control over quality and allowed works to remain on programme despite some challenging weather conditions. A key constraint was the need to redevelop the hospital within the footprint of the existing buildings and clearing areas of the existing site to make way for new buildings while keeping other parts of the hospital running.
The 55,000m2 new build hospital will provide specialist care treatment for over 600,000 people in south east Wales and includes a 24-hour acute assessment unit and emergency department. A 23% programme saving was secured by using DfMA components. Prefabricated and precast elements included manholes, concrete columns, twinwall, lattice planks, hollowcore slabs, delta beams and facade panels. Early engagement allowed us to integrate DfMA and lessons learnt into the design to secure logistical and programme benefits – this included moving the energy centre to another part of the site and constructing the permanent site access roads to enable more efficient logistics.
Expanded have constructed the first new development at Brighton 3T’s (Teaching, Trauma and Tertiary Care Centre). The project has utilised a significant amount of manufactured concrete components from the sister business Explore Manufacturing. Using a team that understand DfMA delivery, they have constructed the two-storey basement and thirteen floors over three wings in over a year. Expanded have also installed 1600 pre-cast concrete cladding components. The Expanded team worked closely with the wider Laing O’Rourke business and sister companies to ensure that the live hospital continues to function throughout the construction work and with minimal disruption to the patients.
The 215,000m2 residential tower, Block F, is the next milestone piece in Imperial College’s major new west London educational campus. It will provide 34-storeys of 192 new apartments in a mix of sizes, including 59 affordable units. Technical challenges were overcome through interactive planning and DfMA solutions for offsite manufacture.DfMA and BIM have been applied extensively; prefabricated welded reinforcement has improved safety, reduced manual handling and guaranteed cover. Strong engineering expertise, early strategy and careful sequencing have unlocked further benefits to the project, including using jumpform to build a concrete core, enabling concurrent installation of risers.
Expanded delivered the structure works for GEIC, a £60m capital investment to strengthen the UK’s position in advanced materials research and development, allowing collaborative university and industry programmes in graphene and 2D materials. GEIC will complement The University of Manchester’s (UoM’s) National Graphene Institute (NGI), which opened in 2015. GEIC is a three-storey 8,400m2 building located on UoM’s North Campus. This state-of-the-art technical facility features two continuous floorplates of modular labs to maximise flexibility of the highly technical, specialised research space. The project involves the construction of laboratories, ancillary offices and conference facilities.
The Henry Royce Institute is a new research facility for University of Manchester, and part of the government’s Northern Powerhouse scheme. Our delivery began with collaboration from RIBA Stage 2 design onwards. We used real-time field data to log progress and manage the quality of components manufactured in-house. We also built a 3D model to maintain accuracy, identify clashes and enable tasks like swept path analysis to be undertaken. During the frame construction, Expanded installed 340 precast columns, 932 lattice planks, 580 twinwall panels and 111 other components, produced at Explore Industrial Park, our in-house precast manufacturer.
Simultaneous delivery of seven secondary schools across the county, which were identified to be in urgent need of renewal. The logistical planning and extensive use of concrete DfMA components enabled new facilities to be delivered as quickly as possible. The time, space and logistics constraints experienced at each site, as well as the challenge of delivering multiple projects across the county with one team, suited a DfMA approach. Construction of the concrete frames was almost exclusively a lifting operation often with over 100 units installed each day; element weights varied between 1.5 tonnes and 19 tonnes.
Working with our parent company Laing O’Rourke, we delivered the piling, two-level substructure and six-storey superstructure for this new building at the University of Oxford. The scheme design of a series of shifted discs and pure geometric circles is developed from the parameters of the site and plot boundaries. Architectural finishes were specified with no obvious joints and surface mounting of services. While concrete for structures like the curved staircases are poured in situ,the shuttering was crafted off site in a controlled environment. Laser- controlled technology was used for the high specification formwork to create smooth curves and edges, atrium walls and staircases.
Expanded are working with Laing O’Rourke on the second phase of the Oxford Biochemistry building for the University of Oxford. Expanded Geotechnical piled the two-storey basement and Expanded Structures have formed the in-situ basement, constructing the lining walls whilst proceeding with excavation. The project has under taken the Digital Build. The Digital Build meant that Expanded could construct the 360-tonne raft slab with 0.005% of waste reinforcement left at the end of its construction. In conjunction with Explore Manufacturing, Expanded have installed the double-storey pre-cast concrete columns and lattice slabs across six floors, reducing the overall programme of works.
We were responsible for the construction of a piled contiguous wall, substructure and superstructure for a 44m high learning facility for the University of Manchester. This is part of a ten-year plan to create a world- class campus. Our package included; construction of a contiguous piled wall and capping beam, followed by reinforced concrete pad foundations, below ground drainage, a 6m deep basement structure and 10,000m2 of reinforced concrete podium slab. The superstructure works included four 44m high jumpformed cores and 33,000m2 superstructure slabs and over 900nr columns with exposed surfaces throughout. The programme included 37,000m3 of concrete, 5,000tn of rebar serviced by four tower cranes and two crawler cranes.
A new six-storey research facility completed in 2019 will centralise biomedical research located on the current campus of a leading University. Working within the parent company frame work of Laing O’Rourke, Expanded managed the design and construction of the structure and played a large part in manufacturing 80% of the structure off site. The extensive use of Digital Engineering and input from the Laing O’Rourke Engineering Excellence Group meant that the project could provide better cost certainty. Direct delivery enabled the project to pull forward activities if an earlier task is completed ahead of plan. This led to a 25-week programme saving.
Expanded constructed 6,800m2 of floor space and the deepest basement in Oxford as part of this project; this deceptively spacious building is as deep as it is tall. It links to the existing Clarendon Laboratory three levels above ground; below, a five-level 16m-deep basement laboratory space has been excavated. Being close to a busy road, the basement labs required a very high degree of environmental controls. Several ‘quiet labs’ were constructed as ‘room within room’, to provide vibration and acoustic isolation. Engineering-led, innovative approach to delivery was supported by our DfMA solution, which reduces onsite traffic and resourcing, with logistical and safety benefits.
We constructed a 5,400m3, belowground, stormwater storage shaft at Hathershaw CSO. This important tranche required a fast-paced £38m programme of works to enhance the river Medlock’s water quality.
Constructing the shaft
The 20m deep and 25.3m diameter shaft is located within a school playing field, accessed through a residential neighbourhood. To minimise disturbances to adjacent properties, we positioned the shaft 30m+ to adjacent properties. The tank fills and empties by gravity, fed by a 1500mm diameter concrete inlet pipe and a 400mm diameter concrete outlet pipe. Our delivery methodology and secant pile offering provided; greater verticality when piling – exceeding targets of 1 in 120 and instead achieving 1 in 1,000, improved programme efficiency – saving six weeks on the critical programme through our inlet portal approach and a safer site – with only four operatives requiring eight days to install the VacFlush column roof.
Our robust, value-for-money solution for Davyhulme involved a commitment to complete construction by 2017, with final handover after optimisation in 2018. Works included installing a new process treatment stream, inlet works, channels, pipelines and distribution chambers to feed six primary settlement tanks, a ten-lane aeration plant and ten final settlement tanks.
A ‘best in class’ solution
In heavy rain, wastewater flows into Davyhulme can reach 30,000 litres per second, the equivalent of 90 tankers every minute. Despite this being UU’s biggest site, our solution – based on ‘best in class’ programme and project management, innovation (particularly in process design and delivery), world-leading wastewater design and performance optimisation – allowed it to remain operational throughout. It also supported UU’s core value of ‘driving innovation’. An £8m green energy scheme also provides bio-gas for electricity generation on site, as well as supplying ‘green’ gas to the national gas grid. This means that Davyhulme WwTW has net-zero operating costs and is power self-sufficient.
LiMA, a joint venture between Laing O’Rourke and Atkins was appointed in December 2017 as main contractor for the Blackburn Batch of projects which includes Blackburn WwTW, Darwen WwTW, Nabs Head Inlet Works and the Darwen Pipeline.
Delivering the project scope
Nabs Head inlet works: construction of two new 10,000m3 blind storm storage tanks, both 102m long by 34m wide. These are filled (at up to 3,000 l/s) from a new CSO pump station and emptied by gravity once there is sufficient capacity to pass the flows onto the main works at Blackburn WwTW. Blackburn WwTW: construction of a new inlet channel and 72,000m3 insitu concrete structure with Nerada aerobic granular biomass technology. The system treats crude sewage that has received preliminary treatment at Nabs Head and is developed to treat the full flow and peak load at the works, ie. a complete replacement and expansion of the existing wastewater treatment plant with a flow to full treatment (FTFT) of 3,000 l/s. The Nerada structure comprises six 12,000m3 reactors; two 800m3 sludge buffers; one 800m3 water level correction buffer; associated aeration and pumping equipment. A Blower building and pipe bridge were constructed to house five blowers with a pipework network to each Nerada cell. Scope also included construction of new; ferric dosing area, UV treatment plant, SAS plant, poly dosing, sludge holding tanks, drum thickeners, lamella area and permanent filter bank. Darwen WwTW: transfer flows under gravity into the adjacent Blackburn drainage catchment, ultimately receiving treatment at the new Blackburn WwTW. Storm water storage at Darwen was increased to 6000m3 by the refurbishment and conversion of existing storm water storage and what would have become redundant primary settlement tanks. The Darwen works now pass forward 517 l/s via the Darwen Transfer Pipeline.
The three-year capital project upgrade commenced in 2021 and is the first major contract awarded as part of their AMP7 schedule and will comprise construction of a completely new inlet works and extend aeration lanes and settlement tanks across four areas. Beckton, which is said to be the largest sewage treatment works in Europe, will also be prepared to receive wastewater from the new Thames Tideway Tunnel, a 25km “super sewer” under the river Thames which is due to be completed by 2024.
Key facts
• Muck shift: 144,000m3
• Reinforcing fixed: 3,000t
• Concrete placed: 23,000m3
• Piles installed: 3,250no
• Precast units installed: 1,074
• Process pipework installed:10km
The biggest infrastructure project ever undertaken by the UK water industry, this is a once-in-a-generation opportunity to make London’s sewerage network fit for the 21st century and beyond.
An enormous engineering feat
Delivering heavy civil engineering, tunneling and complex marine infrastructure on space-limited sites in a busy capital presents an array of logistical and environmental challenges. The main tunnel is a huge undertaking: approximately 25km long, with an internal
diameter of between 6.5m and 7.2m, equivalent to the width of three London buses. The depth of the tunnel is between 35m in west London and 65m in east London.
Constructing shafts and a river wall
Expanded constructed rotary bored secant piles and rotary bored piles for the construction of the two shafts and river wall as part of the Albert Embankment Foreshore Tideway Project. The interception chamber shaft located by the Vauxhall Bridge connects the exiting Clapham and Brixton sewer outlets and the 48m deep circular shaft, located in Cofferdam 1 in front of Camelford House, connects the main Tideway Tunnel built under the river Thames.
Extremely restricted site
This was a constrained site, with Cofferdam 2 isolated from any road supply for all deliveries. To overcome this all plant, piling equipment and steel reinforcement were delivered to site by barge and lifted into site, always considering the high and low tides of the river to schedule the deliveries.
Key facts
• Cofferdam 1: Installation of 66no. 1200mm diameter contiguous bored wall piles and a challenging 66Nr 1300mm diameter hard-hard secant piles 27m deep fully cased, allowing the excavation of the circular shaft.
• Cofferdam 2: Installation of 147no. 750mm diameter firmhard wall as part of the interception chamber as well as 17no. 750mm diameter bearing and tower crane piles.
• The total bored length on the project was just over 6000m requiring approximately 5500m3 of concrete.
London’s ‘super sewer’: cleaner, greener and more efficient waste processing for our world-leading capital city.
Piling and concrete contractor for the biggest infrastructure project ever undertaken by the UK water industry, this is a once-in-a-generation opportunity to make London’s sewerage network fit for the 21st century and beyond.
Delivering heavy civil engineering, tunnelling and complex marine infrastructure on space-limited sites in a busy capital presents an array of logistical and environmental challenges. The main tunnel is a huge undertaking: approximately 25km long, with an internal diameter of between 6.5m and 7.2m, equivalent to the width of three London buses. The depth of the tunnel is between 35m in west
London and 65m in east London.
Key facts
• Installed over 150 secant wall piles using one piling rig and four 7500mm diameter rotary bored bearing piles and two drilled shafts
• The total bored length on the project was approximately 2715m requiring approximately 1600m3 of concrete
A unique, angular steel and glass spire, rising 224m high with spectacular views over London. The building’s tapering profile reflects the planning requirement to respect the view of St Paul’s Cathedral. Expanded were the UK’s first contractor to use precast concrete floor modules in a high-rise building. These are assembled off site at our own Explore Manufacturing facility. The planks are delivered to site in modular units and craned into position to construct the building’s floor plates. This is a major break from traditional construction and avoids the risks to health and safety, and noise and disruption normally associated with working at height and concrete works.
The Brunel Building is a Paddington landmark, designed with an external steel diagrid structure, enabling flexible, column-free office floors. The building accommodates 240,000ft2 of offices fronting the Grand Union Canal, opposite Paddington station, and providing a new public waterside. Additionally, 100 apartments have been built, divided from the commercial building by a full-length concrete core. Expanded constructed the concrete finish jump-form cores, along with the special diagrid feet and two storey basements. A BIM-enabled collaborative design-management process enabled certainty for all parties. There was an element of architectural pre-cast concrete which clad the face of a core. The project was Highly Commended by The Concrete Society in 2018.
No. 2 St Peter’s Square was a single-stage design-and-build contract which provided 15,000m2 of BREEAM Excellent, Grade A office accommodation over 12 floors, basement parking for 70 vehicles and 500m2 of retail space. Expanded re-engineered the two-storey basement to de-risk its construction and provide early access for materials storage. Additionally, there was a requirement to install long span cellular beams, which weighed up to 30t. Because of restriction by the operational Metro Line, Expanded instead utilised in-house Temporary Works Department to design a method of placing a 250t crane within the building footprint, through back propping the lower floors.
Expanded worked alongside Equinox during the PCSA for one of their newest data centre projects, LD7, provided the opportunity to use the experience from delivering the LD4, 5 and 6 data centre projects and raise the bar even further. This enabled us to plan the strategy for LD7, mitigating potential risk way before construction started on-site. In-house delivery on the major packages has allowed us to achieve an accelerated programme. Each installation has been digitally engineered to design out risk before we start on site. We have increased our DfMA offer and maximised our digital engineering to enhance construction and assist future FM.
Laing O’Rourke constructed this 13-storey block to provide 220,000ft2 of prime Grade A commercial office space in Glasgow city centre. Although the building was originally planned as an in situ post-tensioned concrete frame, we could influence the outcome such that almost all the superstructure is of manufactured – mostly precast concrete – components. Our methodology involved double-height columns with beams, hollowcore planks and a structural topping. Cores are a combination of in situ reinforced concrete and twinwall, while the facade includes polished precast concrete panels and glazed curtain walling. In terms of piling and groundworks, the top-down basement used plunge columns, eliminating the need for baseplates and holding- down bolts.
Expanded constructed the substructure and concrete frame for a 10-storey block that provides 300,000 sq. ft. of office space, housing cinema rooms, retail units, and a private members’ club. The Plot A works were adjacent to the existing BBC Worldwide building, which remained in use – therefore strict noise and working hour controls were in place. Expanded constructed the core using a jump form system, with the Reckli form liner used to produce the bespoke timber board mark effect. Our scope of work also included sheet piling, jumpform cores, post-tensioned slabs, precast columns. Expanded were Highly Commended by The Concrete Society in 2018 for this project.
Expanded are working with Lendlease to supply some key architectural pre-cast concrete to the new Google London Headquarters in Kings Cross. Consisting of eleven storeys and located on the slender patch of land between Kings Cross Railway and Pancras Square, the building will eventually accommodate 1 million square feet and up to 7,000 Google employees. Sister business Explore Manufacturing are producing the bespoke slab and stair elements at their facilitiy in Worksop, near Sheffield.
A two-stage BREEAM Excellent design-and-build project for a new- build high-quality office and design facility across 67,000m2. The design incorporated a steel frame with integrated precast concrete basement walls and exposed concrete floor slabs and timber Glulam roof beams. Expanded was engaged from the outset as part of Laing O’Rourke’s tender team for the delivery of piling, plunge columns, substructure, drainage, in situ and precast concrete (walls, floors and stairs). Similarly, Expanded Piling was engaged at an early stage for piling, including plunge piling. The team could offer a single-phase option, which significantly reduced the overall programme period and cost to the client.
Expanded supported Laing O’Rourke as the main contractor on a two-stage design-and-build project for a 21,000m2 noise, vibration and harshness specialist automotive testing facility, part of JLR’s vision to create one of the world’s foremost automotive product, engineering and design sites. Expanded (piling and structures) and Explore Manufacturing (components) worked alongside the EnEx.G to develop an optimal solution for the acoustically isolated test cells that will put JLR’s vehicles through rigorous, state-of-the-art tests before they can hit the road. The solution developed for the 25 test cells to meet acoustic and vibration criteria comprises seismic mass block foundations, structural steel, and up to 8m-high twinwall components.
The Post Building comprises 44,000m2 of mixed-use development over 12 floors, including mezzanines. The scheme design required retention and incorporation into the design of the existing basement and three floors of existing structure over approximately a third of the building footprint. The Post-Building comprised of a structural refurbishment to the existing composite deck structure and construction of a 9-storey pre-cast concrete residential block. The structural refurbishment consisted of a composite metal deck system that was tied into sections of existing retained structure to tailor the new building layout to the required footprint. The Residential block consisted of pre-cast lattice planks, columns and twinwall which were manufactured at Explore Manufacturing.
Expanded, as part of Laing O’Rourke as Principal Contractor, were invited to replace the original contractor to deliver the shopping centre’s new 400,000ft2 extension, after the successful completion of the Nottingham Victoria Centre’s refurbishment. We also worked closely with the demolition contractor, Keltbray, to ensure that all temporary works were integrated effectively with the permanent works, thereby ensuring a smooth, cohesive delivery. We used innovative construction methods, including precast concrete components and modular services distribution, which reduced site labour levels as well as minimise noise pollution, dust and nuisance.
Expanded completed the design and construction of the shell and core of a three-storey retail centre, two-storey basement car park and a new residential apartment block, all to a BREEAM Excellent standard. Our in-house delivery team’s wealth of recent retail experience was a key factor in our appointment. For the new John Lewis store, we applied a DfMA philosophy and used offsite manufacturing for the precast concrete frame and facade, which features masonry panels. We exceeded the client requirement to save 25,777t of CO2 of embodied carbon during construction by over 35% through intelligent design and procurement. More than 99.98% of all construction waste was successfully diverted from landfill.
A 1.7millionft2 mixed-use development in the centre of Edinburgh, replacing the existing St James Centre with 850,000ft2 of retail, leisure and hotel facilities and 152 new homes. Our Engineering Excellence Group have provided technical advice to de-risk delivery of this major project. Our input introduced a DfMA approach to deliver the extensive subterranean car park and feature stone clad facades, delivering over 4,000 components. The extensive basement was engineered to remove intrusive props through rock anchoring and a progressive excavation sequence. We have also utilised 4D modelling to plan and validate the complex underpinning works to the John Lewis store.
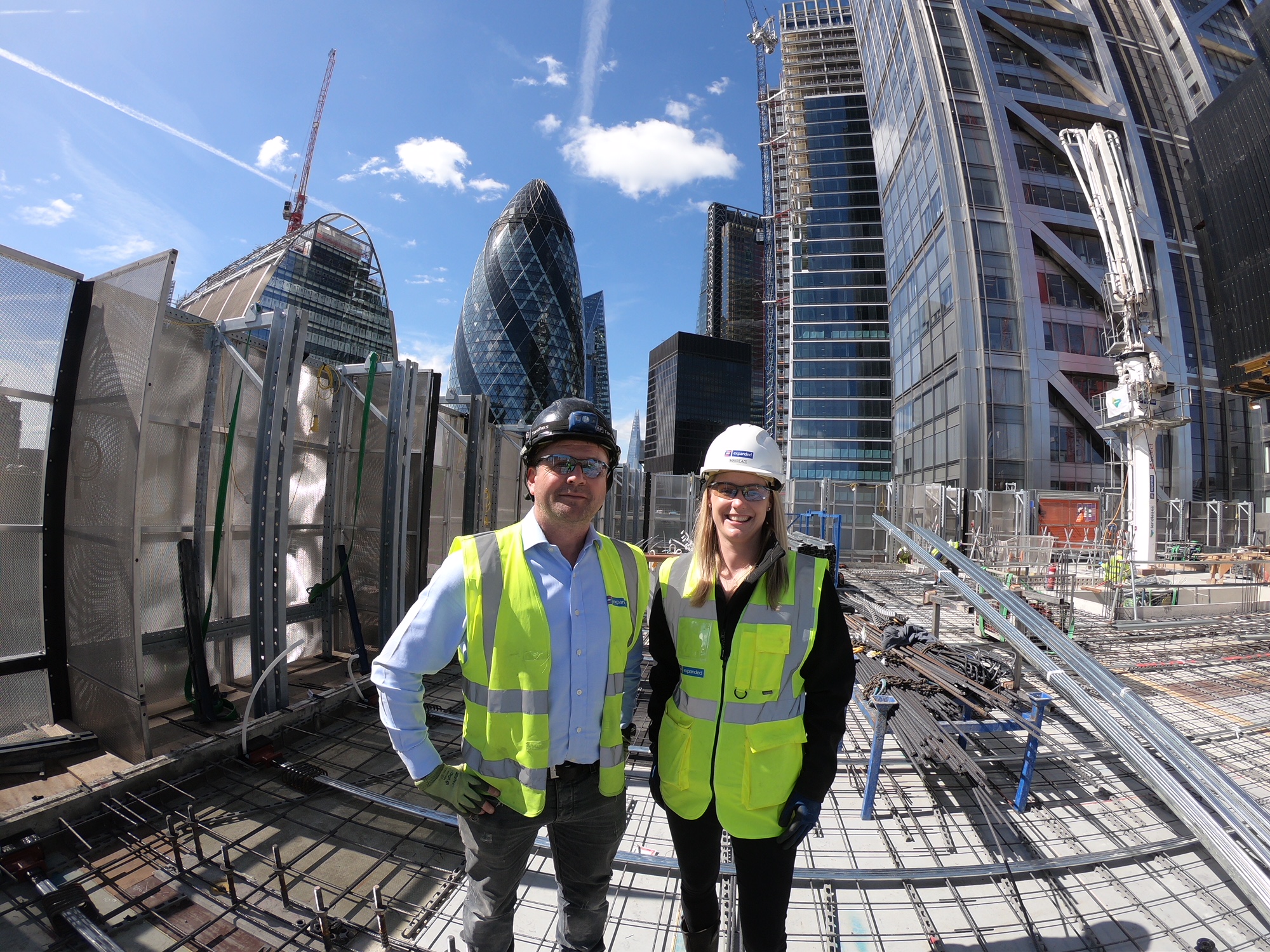